Manufacturing Technologies
Metal-ink printing and photonic (IPL) sintering
We utilize the printing capability to create electronics on flexible substrates. In high throughput roll-to-roll (R2R) and sheet-to-sheet (S2S) manufacturing environments, direct print technologies (gravure, flexography, and ink-jet) provide lower cost and larger printing area. The use of metallic nano inks, where metal nanoparticles are dispersed in printable carriers, has attracted great interest because of inherently higher electric conductivity and mechanical durability. However, unlike organic-based electronic materials, metallic nano inks require a sintering process in order to form conductive films. We studied a novel photonic sintering process using a Xe-flash lamp. The advantages of the Xe-flash photonics sintering are: (1) Little impact on polymer substrate – Unlike the conventional furnace whose temperature is detrimental to the substrate, room temperature sintering is achieved through selective heating of nanoparticles over the polymeric substrates; (2) Scalable manufacturing – the photonic process can be applied on much larger areas at once in comparison to laser-based spot sintering technique. (Reference: Ryu, J., Kim, HS. & Hahn, H.T. Reactive Sintering of Copper Nanoparticles Using Intense Pulsed Light for Printed Electronics. J. Electron. Mater. 40, 42–50 (2011). https://doi-org.prox.lib.ncsu.edu/10.1007/s11664-010-1384-0)

Functionally graded materials by 3d printing – modeling and implementation
As AM technology matures, the number of printable materials has greatly increased. Research into new materials and the effects of complex structural arrangements has increased tremendously both from industry and academia looking for novel applications to this technology. AM technologies are capable of locally tuning material properties to generate Functionally Graded Materials (FGM). Artificially engineered FGMs have been applied to create aerospace structural materials, lightweight concrete structures, and bone-mimicking implants. However, the capability of conducting meaningful computer simulations for FGMs is limited mainly due to the lack of information regarding the material properties and appropriate material models. In our recent study, we developed mechanical models of the printed materials and validated the model-based computational analysis by comparing them with physical tests. (Reference: Salcedo, Eduardo, et al. “Simulation and validation of three dimension functionally graded materials by material jetting.” Additive Manufacturing 22 (2018): 351-359.)

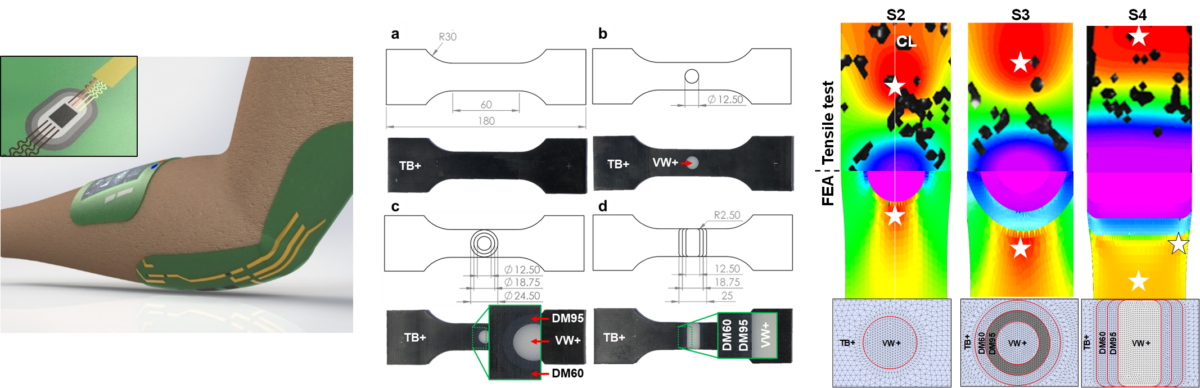